Company Information

Iggesund Paperboard Head Office
Iggesund Paperboard AB
SE-825 80 Iggesund
Sweden / Sverige
Phone: +46 650 280 00
Fax: +46 650 288 00
Press contact
Therese Rahm
Communication Manager
Phone: +46 70 595 56 10
Company Information

Iggesund Paperboard Head Office
Iggesund Paperboard AB
SE-825 80 Iggesund
Sweden / Sverige
Phone: +46 650 280 00
Fax: +46 650 288 00
Press contact
Therese Rahm
Communication Manager
Phone: +46 70 595 56 10
About Iggesund Paperboard AB
Iggesund Paperboard is part of the Swedish forest industry group Holmen, one of the world’s 100 most sustainable companies listed on the United Nations Global Compact Index. Iggesund’s turnover is just over €500 million and its flagship product Invercote is sold in more than 100 countries. The company has two brand families, Invercote and Incada, both positioned at the high end of their respective segments. Since 2010 Iggesund has invested more than €380 million to increase its energy efficiency and reduce the fossil emissions from its production.
Iggesund and the Holmen Group report all their fossil carbon emissions to the Carbon Disclosure Project. The environmental data form an integral part of an annual report that complies with the Global Reporting Initiative’s highest level of sustainability reporting. Iggesund was founded as an iron mill in 1685, but has been making paperboard for more than 50 years. The two mills, in northern Sweden and northern England employ 1500 people.
The Iggesund Mill
Making the world’s best paperboard is easy. You need water, carbon dioxide and sunlight to grow a seedling into a tree. Then you need sustainable forest management that can deliver first-class timber. There must be a pulp mill and a paperboard mill, and then distribution channels to get the paperboard to everyone who wants to use it. Most important of all, though, to the manufacture of Invercote are the skilled professionals who do their best – people who are proud of what they achieve and do not compromise on the quality of their work. Iggesunds Mill has traditions stretching back to 1685. Throughout that time dedicated individuals have done their utmost to use the renewable forest to benefit other people.
A world-class mill
Iggesund Mill (including Strömsbruk Mill) in Sweden is one of the most advanced, fully integrated pulp and paperboard mills in the world. Not least thanks to our long term majority owner, we have very well invested mills. There are many benefits having an integrated saw mill – we manage raw material together and we can use all the waste from their production to either make pulp or energy. In return we feed the saw mill with steam used to dry the timber. At Iggesund Mill, 100% of the pulp used to make Invercote is produced on location and pumped wet to the board machine. This means that we use no market pulp. Not drying the pulp preserves some mechanical properties of the fibres.
This advanced technology – hundreds of metres of paperboard machines – is controlled by employees with various forms of special expertise. The machines work around the clock and year round to produce tonne after tonne of dazzling white paperboard. Technical perfection and numerical control processes are all well and good but for excellent results you also need team spirit and a good working atmosphere. Invercote’s unique properties are the result of the interplay between expertise, a positive spirit and cutting-edge technology.
Actively investing in bioenergy
In 2012 the new recovery boiler was inaugurated at Iggesund Mill, an investment made possible by the long term perspective of our majority owner. With it in operation, the mill produces all the heat it needs, and can also provide district heating to the nearby community. It also produces nearly all the electricity needed for the mill, and is connected to the grid to be able to output excess electricity if needed. As the new boiler was trimmed into operation, it drastically reduced a lot of emissions between 2013 and 2014: fossil CO2 by >85%, particles by ~45% and sulphur by ~35%
With the installation and trimming of the new recovery boiler, emissions to air have reduced drastically from already low levels – graph being updated shortly. Measurements have shown that only 1% of particles in the air of Iggesund village comes from the mill. The majority of particles comes from domestic fire places and cars.
Care for our customers and their businesses
Paperboard must be there when the customer needs it. All the quality features in the world are meaningless if the deliveries don’t arrive in time. Delivery precision is a high priority. A maritime transport system guarantees overseas customers receive shipments with the lowest possible environmental impact. The service doesn’t stop there. Every tonne of Invercote comes with access to documentation and knowledge about how to make best use of the paperboard. The knowledge and market-based technical support provided by Iggesund, help customers to achieve dazzling end results and optimal production economics.
Publications
Handwritten resistance to smartphone use
Published on
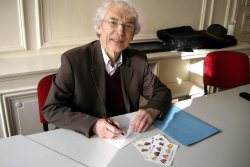
/INS. How can we persuade schoolchildren and teenagers to loosen their grip on their smartphones and write by hand instead? Bernard Bouvet is chairman of the Union Professionnelle de la Carte Postale, (UPCP), an advocacy organisation for the postcard industry in France. He may not have all the answers but he is at least practising active resistance. In recent years UPCP has put both itself and postcards on the map by creating the writing week Semaine de l’écriture, which aims to teach schoolchildren the value of writing texts by hand. Iggesund Paperboard has supported the campaign since its inception by providing materials for the postcards used in the various writing activities.
Iggesund further reduces carbon emissions
Published on
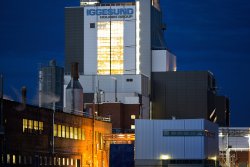
/INS. Iggesund Paperboard’s Swedish pulp and paperboard production facility, Iggesund Mill, reduced its fossil carbon dioxide emissions by 86 per cent from 2013 to 2014 from what was already a low level. The reduction is partly due to the investment in a new recovery boiler, which was completed in 2012.
Invercote G from Iggesund : Upgraded for better digital printing
Published on
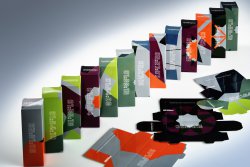
/INS. “We’re seeing almost an explosion of digitally printed folding cartons. For a company like ours which offers stiff paperboard of the highest quality this is a terrific development,” comments Fredrik Lisinski, who is responsible for developing Iggesund Paperboard’s sales to the digital print market.
Iggesund invites international designers
Published on
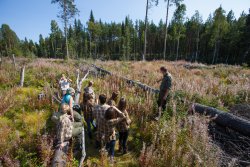
/INS. Iggesund Paperboard, manufacturer of the world-leading paperboard Invercote, is inviting designers from all over the world to participate in a unique learning experience. From those who apply, 20 will be chosen to join the Iggesund Design Experience in Sweden in June 2015.
Virgin fibre a necessity in chocolate packaging
Published on
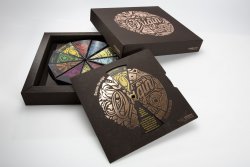
/INS. “When we choose the paperboard for chocolate packaging, the decisive factor is taste and odour neutrality. Of course the paperboard must be suitable for the construction we have chosen but if we do not minimise the risk of the chocolate acquiring an off-taste from the packaging material then the rest does not matter.”